Here's my official CYA statement. Before you do anything at all with RTV Silicone, Casting Resin or any other hazardous chemicals be damn sure you have the correct protection and follow the correct safety procedures while handling the material. All chemicals you buy should have available safety precaution data sheets. I'd suggest reading them thoroughly and don't dare deviate from the recommendations. Playing roulette with your health isn't a good idea. Don't blame me if you splash casting resin in your eye and it hardens before you can say boo. I always work with protective goggles, full respirator, lots of paper towels on hand and a new pair of latex gloves. Don't get lazy and don't try to save a buck by cutting back on protective gear. If you seriously want to get into casting, you're going to be spending a few hundred bucks at least to get the proper equipment and RTV silicone will run you about 30 bucks for half a litre. (there's over one litre in the mold below)
Welcome to the making of "Jenna"
Jenna is the name I gave to the sculpture you'll see below in this step by step mold making process. If you're interested in sculpting and casting, this step-by-step will give you a great headstart on one way to go about it. When I created the mold for Jenna, I had already had the experience of using RTV silicone many times before. I've also got 3+ years of casting research under my belt. I'd suggest that my process here is not the final be all and end all of mold creation as you will need to do your own research and find out all you can before you start. Then once you've answered all your own questions you should try casting something you're not too attached to as a test. No amount of reading will take the place of honest-to-goodness experience. You're gonna break a few eggs before you're able to make a good omelet...as they say. Just don't rush it and break you're prize dodo bird eggs before you know what you're doing.
Well, This should really be called "The Casting of Jenna" As I didn't take any progress shots of the sculpting process on this one. (I promise I will take great in sculpting progress shots of the next one...)
Making the mold.
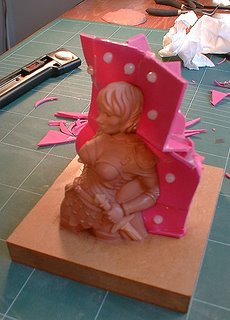

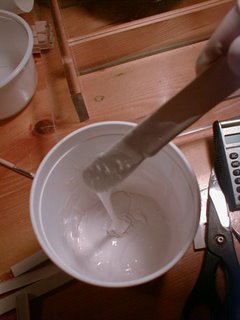
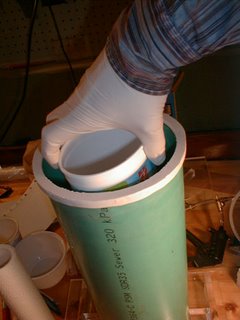
...I place the RTV into a vacuum chamber. Vacuuming it pulls the air bubbles out of the mixture leaving a clean and bubble-free batch of silicone ready for careful pouring.

The Casting Station.
This is where I do all my casting. On a big table in a space that can get messy. In a well ventelated garage (I still use the respirator). See the road speed sign on the side? When casting, I follow it.... Work slowly and carefully and you'll screw up much less and save money. Vacuum chambe in the centre, vacuum pump to the right of that.
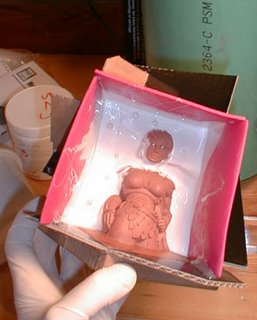
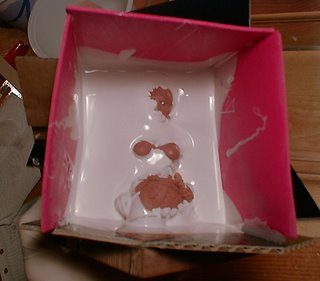
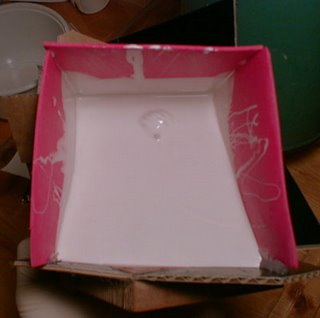


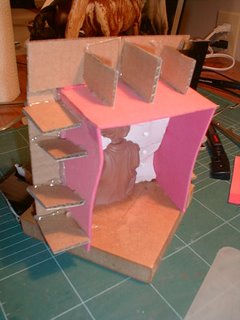
The most important step... I applied vaseline to the entire exposed surface of silicone. If this step is forgotten, the new silicone will CHEMICALLY BOND with the first side and you'll have a big block of silicone that you can't pull apart. That's bad. Very bad.
All set to pour.
I mixed up a new batch of RTV for this side going through the same vacuuming and pouring process as for the first side.

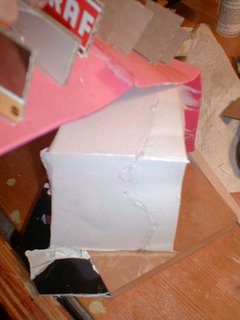

The cleaned up and completed mold with sculpture embedded inside.


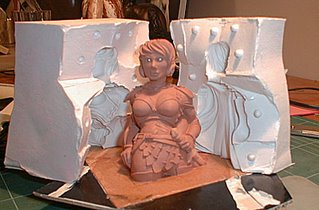
Hope you learned something.... about casting today!
Here's what it took me to to get to this point:
6 days of constructing, pouring and waiting!
3 years of research, buying equipment, building, testing and learning!
50 hours of sculpting!
Peace and Balance - and happy casting!
~The Art Ninja~
"You don't have to be great to get started, you do have to start to become great"